當前位置:
天津 恒永興金屬材料銷售
有限公司 >湘潭本地行業頻道
鋁合金型材,精密管來圖加工定制
更新時間:2025-01-27 04:05:36 瀏覽次數:3 公司名稱:天津 恒永興金屬材料銷售 有限公司
以下是:鋁合金型材,精密管來圖加工定制的產品參數
產品參數 | |
---|---|
產品價格 | 358 |
發貨期限 | 電議 |
供貨總量 | 電議 |
運費說明 | 電議 |
品牌 | 恒永興 |
規格 | 齊全 |
價格 | 電議 |
以下是:鋁合金型材,精密管來圖加工定制的圖文視頻
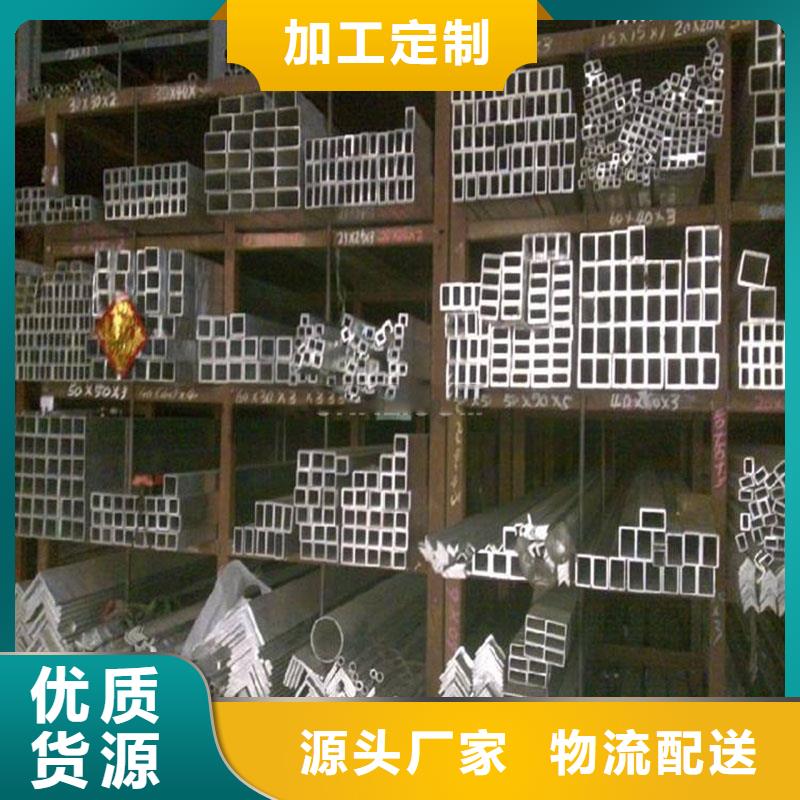

鋁合金型材,精密管來圖加工定制,恒永興金屬材料銷售
有限公司為您提供鋁合金型材,精密管來圖加工定制,聯系人:李經理,電話:022-86869388、18802286588,QQ:554918566,請聯系恒永興金屬材料銷售
有限公司,發貨地:天津北辰區雙街鎮京津路西(北方實業發展有限公司內)發貨到湖南省 湘潭市 雨湖區、岳塘區、湘鄉市、韶山市。 湖南省,湘潭市 湘潭市,湖南省轄地級市,簡稱潭,因盛產湘蓮而別稱“蓮城”,又稱“潭城”,總的地貌輪廓是北、西、南地勢高,中部、東部地勢低平。截至2023年,全市轄2個區、1個縣,代管2個縣級市,總面積5006平方千米。截至2022年底,全市常住人口270.27萬人。
想知道鋁合金型材,精密管來圖加工定制產品為何如此受歡迎?觀看視頻,答案自在其中。
以下是:鋁合金型材,精密管來圖加工定制的圖文介紹
恒永興金屬材料銷售 有限公司生產設備精良,工藝先進,檢測手段齊全,技術力量雄厚; 湖南湘潭低中壓鍋爐管產品共有三大系列、三十多個品種,并承接各種非標產品的設計和制作,規格齊全,質量保證, 湖南湘潭低中壓鍋爐管產品銷往全國各地,受到廣大用戶的一致好評。
當電解槽實際電解溫度高于正常控制的電解溫度上限時,我們稱該電解槽為熱槽或進入了熱行程。從能量平衡的角度,形成熱槽的原因為熱收入增加,或因熱支出減少,或二者同時存在。決定電解槽熱收入的主要因素有槽工作電壓、陽極效應、系列電流、電解質電阻等。影響電解槽熱支出的主要因素有保溫料厚度、鋁水平等。因熱收入和熱支出的某項或幾項因素發生改變而導致電解槽溫度上升的熱槽,常稱做普通熱槽。而由于各項技術條件匹配不合理、槽膛嚴重畸形等多重深層次誘因引起的病槽,水平電流增加,二次反應加劇,電流效率明顯下降,本該轉變為化學能的電能大量以熱能釋放出來,使槽溫上升,形成熱槽,我們把這種熱槽稱做異常熱槽。具體分析,可能形成熱槽的原因主要有以下幾種:(1)極距保持過高,電解質電阻壓降增加,槽電壓偏高,槽內熱收入過多。造成極距過高有兩種可能原因,一種是電壓測量儀表有誤差,測量值低于實際電壓值,計算機按測量值調整極距,使極距控制偏高;另一種是人為地提高槽電壓沒有及時降下來。(2)極距過低,引起二次反應加劇。二次反應放出大量熱量,使電解槽溫度上升。(3)電解槽內鋁水平過低,鋁量少,槽底散熱量減少形成熱槽;或因電解質水平過低,液體電解質量少,氧化鋁溶解能力下降,槽底產生大量沉淀,引起槽底發熱;電解質水平過低,電解槽熱穩定性也變差,這也容易引起熱槽。(4)電流分布不均勻,局部電流集中,形成局部過熱現象。(5)陽極效應處理不及時,或處理方法不當,效應持續時間過長,造成槽溫上升。(6)由于冷槽處理不及時或處理不得法而轉變成熱槽。因為冷槽因溫度低而電解質萎縮,氧化鋁溶解能力降低,如果得不到及時處理,會形成大量沉淀,導致槽底發熱,加之效應頻發,效應電壓高,槽溫上升,進而轉化成熱槽。電解槽進入熱行程會有以下外觀特征:(1)火苗黃而無力,電解質物理化學性質發生明顯改變,流動性極好,顏色發亮,揮發厲害,陽極周圍電解質沸騰激烈,電流效率很低;(2)炭渣與電解質分離不清,在相對靜止的液體電解質表面有細粉狀炭渣漂浮,用漏勺撈時炭渣不上勺;(3)陽極著火,氧化嚴重;伸腿變小,槽底沉淀增多;(4)殼面上電解質結殼變薄,下料口結不上殼,多處穿孔冒火,冒“白煙”;(5)槽膛遭到破壞,部分被熔化,電解質溫度升高,電解質水平上漲,鋁水平下降,電解質摩爾比升高;測兩水平時,電解質與鋁液之間的界線不清,而且鐵釬下端變成白熱狀,甚至冒白煙;(6)電解質對陽極潤濕性很差,槽電壓自動上升,陽極效應滯后發生,效應電壓較低,不易熄滅;(7)嚴重熱槽時,電解質溫度很高,整個槽無槽幫,無表面結殼,白煙升騰,紅光耀眼;電解質黏度很大,流動性極差,陽極基本處于停止工作狀態,電解質不沸騰,只出現蠕動。這種狀態在生產中稱之為“開鍋”現象。電解槽進入熱行程,要及早發現,及時處理。首先要分析屬于普通熱槽還是異常熱槽。對于普通熱槽的處理,要分析熱槽產生的原因,針對不同誘因采取不同措施:(1)因設定電壓過高產生的熱槽,將電壓適當降低即可減少電解槽體系中的熱收入;(2)因槽內鋁水平過低引起的熱槽,可采取減少出鋁或向槽內加入固體鋁的方法提高在產鋁量,增加熱的傳導和散失;(3)摩爾比高引起的熱槽,適當多添加氟化鋁,降低摩爾比;(4)保溫料厚的要適當減薄保溫料;(5)槽內炭渣量大的要做好撈炭渣工作,始終保持電解質清潔;(6)還要適當保持較高的電解質水平,增加電解槽的熱穩定性。對于異常熱槽的處理,關鍵仍然是要認真檢查槽況,正確判斷產生熱槽的原因,對癥實施處理措施,否則不但不能使熱槽恢復正常,反而能引起更多嚴重后果。一般檢查的項目包括:首先校對電壓測量儀表是否存在誤差,然后檢查電解質水平、鋁水平、槽底沉淀和槽膛情況、槽電壓保持情況、陽極電流分布情況;查看工作記錄,了解該槽加工和效應情況。根據收集到的息做出判斷,擬定并實施對癥處理辦法:(1)因極距過低,二次反應增加引起的熱槽,首先要將極距調至正常,減少二次反應,增加發熱量的因素。(2)槽內沉淀多,或因槽底結殼造成槽底壓降大,引起槽底發熱而產生的熱槽,要先處理沉淀,如通過扒沉淀,或調整技術條件逐步槽底沉淀。(3)因電流分布不均勻形成的熱槽,要查找電流分布不均勻的原因并采取措施。如因陽極某部位與沉淀接觸引起的偏流,要處理該部位的沉淀;如因陽極長包或掉塊引起的偏流,要盡快處理異常陽極。(4)由于電解質電阻大引起電解質過熱而形成的熱槽,可以短時間打開大面結殼,使陽極和電解質裸露,加強電解槽上部散熱;同時向槽內添加氟化鋁和冰晶石粉的混合料。混合料的熔化將吸收大量熱量,降低槽溫;添加的氟化鋁則降低摩爾比,降低初晶溫度并改善電解質的導電性能。(5)嚴重的熱槽可以采取倒換電解質的方法來降低槽溫;需要注意的是,絕不能用添加氧化鋁來降低槽溫。(6)因病槽引起的熱槽,要先采取措施使電解槽槽況穩定后,再處理槽溫高的問題;由冷槽惡化轉變成的熱槽,要分析判斷原因,參照以上所述方法及時處理。熱槽好轉的標志是陽極工作正常、電解質沸騰有力、表面結殼均勻完整、炭渣分離良好。這時再逐漸降低槽工作電壓,并配合恢復極上保溫料,根據具體情況,緩緩撤出鋁液,槽底沉淀,使電解槽穩步恢復正常運行。熱槽好轉后,往往槽底仍存在較多沉淀,尤其是嚴重熱槽,沉淀層厚度大。但這種沉淀與冷行程的沉淀不同,因其槽底溫度高,沉淀疏松不硬,容易熔化。在恢復階段,只要嚴格控制電壓下降程度,合理掌握出鋁量,適當保持效應系數,沉淀即可,電解槽很快就能轉入正常,但若控制不好,也很容易反復。因此,恢復階段必須精心調整各項技術條件,時刻注意槽況變化,確保電解槽平穩轉入正常運行。
鋁型材散熱器生產工藝:首先貼膜不能直接貼在鉻化層上,否則會影響膜的附著力;其次,貼膜后要及時噴涂不能停放時間過長,否則容易導致貼膜脫落,嚴重時還要重新貼膜;再次是撕膜時要控制流平時間,不能貼膜后馬上撕膜,這樣會對產品質量帶來一定的影響;*后是兩種顏色的噴涂順序要根據具體情況確定,既要考慮到兩次固化,又要考慮到遮蓋效果。貼膜質量控制:散熱器鋁型材質量控制中貼膜質量很重要,若貼不好,會導致噴涂困難,如貼膜的張力不大、壓緊程度要控制好;對形狀復雜的部位要分開貼膜,貼膜后要檢查貼膜是否貼牢。否則將會給噴涂帶來麻煩。影響噴涂質量。公司生產的鋁型材產品均由專業的技術人員嚴格把關,并擁有專業的生產設備,保證質量問題,客戶可放心選購我廠產品。鋁型材散熱器的貼膜材質:首先要對貼膜材質合理選擇,根據散熱器鋁型材產品的要求、表面處理方式,選擇相應的貼膜,同是還要考慮貼膜上的膠對鋁型材表面質量的影響。
縮孔是鋁合金壓鑄件常見的內部缺陷,常出現在產品壁厚較大或者易形成熱點的位置。一般來講,只要縮孔不影響產品的使用性能,都以合格的方式來判定。然而,對于一些重要部位,如汽車發動機汽缸體的冷卻水道孔或潤滑油道孔,出現縮孔是不允許判定合格的。
某企業的一款鋁合金制發動機曲軸箱,采用布勒28000kN冷室壓鑄機鑄造,材質為ADC12合金,成分見表1。鑄件毛坯質量為6.3 kg,后工序進行X射線探傷時發現第二個曲軸軸承孔油道出現縮孔,離油道約8 mm,存在較大的漏油風險。據統計,2017年該位置的縮孔報廢率為5%,經過一系列的探索,成功地將廢品率降低為0.2%。本課題從鋁合金壓鑄件縮孔的形成機理[1-5]和鑄造條件兩方面出發,分析鑄件產生縮孔的原因,尋求改善措施,以期為日后解決鋁合金壓鑄件縮孔問題提供參考。一、鋁合金壓鑄件縮孔形成機理及形態--縮孔形成機理:導致鋁合金壓鑄件縮孔的原因較多,追溯其本源,主要是鋁合金從液相向固相轉變過程中鋁液補縮不足而導致。常見的縮孔原因有:①模溫梯度不合理,導致鋁液局部收縮不一致。②鋁液澆注量偏少,導致料餅薄,增壓階段補壓不足。③模具存在熱結或尖銳區域。④模具的內澆口寬度不夠,面積較小,導致鑄件過早凝固,增壓階段壓力傳遞受阻、鋁液無法補縮。⑤鑄造壓力設置過低,補縮效果較差。圖1為鋁合金鑄件縮孔形成的示意圖。鑄件縮孔形態:縮孔是一種鋁合金壓鑄件乃至鑄件常見的內部缺陷,常出現在產品壁厚較大、模具尖角和模溫溫差較大等區域。圖2為某款發動機曲軸箱縮孔形態,縮孔呈似橢圓狀,距離軸承油道孔約10 mm,內壁粗糙,無光澤。縮孔區域鑄件壁厚較大,約為22 mm;油道孔銷子前端無冷卻水,模溫較高。汽車發動機曲軸的兩大軸頸(主軸頸和連桿軸頸)工作載荷較大,磨損嚴重,工作時必須進行壓力潤滑。在此情況下,軸頸的油道孔附近若存在縮孔,將會嚴重影響潤滑效果。二、縮孔相關對策:鋁合金壓鑄件產生鑄造缺陷的原因有產品本身的結構特征、模具設計得澆注系統及冷卻系統設計不合理、工藝參數設計不合理等原因[1~4]。根據常見的鑄造缺陷原因以及鋁合金鑄件缺陷處理流程,探索解決鋁合金壓鑄件厚大部位縮孔的相應對策。前期分析及對策:鑄件縮孔的前期分析從容易操作的工藝參數出發,通過現場測量及觀察,測得模具內澆口厚度為4 mm,計算的內澆口速度為40 m/s,產品壁厚*薄處為4.6 mm;料餅厚度為25 mm;鑄造壓力為60MPa。由經驗可知,模具設計符合產品的結構特征,模具澆注系統應該不存在增壓階段補縮不足的問題。但是,增壓階段的鋁液補縮與料餅厚度和增壓壓力有直接的關系,合適的料餅厚度與鑄造壓力才能形成內部組 織致密的鑄件,因此,可以懷疑縮孔是由鑄造壓力偏低和料餅偏薄而導致的。前期鑄件縮孔的對策分為兩個:①鑄造壓力由之前的65MPa提高至90MPa;②料餅厚度有原來的25 mm調整為30 mm。采用上述措施后,經過小批量專流驗證,縮孔率由5%減低為4.8%,效果不明顯,說明工藝參數不是引起鑄件縮孔的主因。中期分析及對策:由于引起鑄件縮孔的本質原因是鋁液凝固時補縮不足而導致,而模具溫度分布不均容易導致鋁液凝固順序不合理,從而補縮不足,因此,中期對策分析主要從確保合理的模具溫度入手。由產品3D模型可知,鑄件縮孔處壁厚為22.6mm,壁厚較大,容易引起較高的模具溫度。鋁液凝固時,壁厚較大鑄件內部鋁液由于溫度較高,尚處于液相或者固液混合相,而此時內澆口進行補縮的通道可能已經凝固。這樣,在增壓階段鑄件無法進行鋁液補縮,從而有形成縮孔的可能。為確保合適的模具溫度,采用熱成像儀測得脫模劑噴涂后模具*高溫度為272℃(見圖3),高于正常的模具噴涂后溫度,其他區域模具溫度及其分布整體正常。因此,需要降低縮孔處模溫。另外,測得此處冷卻水孔底部距離模具型腔表面距離較大為20 mm,因為較大的熱傳遞距離會降低模具的冷卻效果,所以需要對冷卻水孔進行更改。為降低縮孔處模具溫度,主要采取3個方法:①改善模具冷卻系統。將縮孔附件的冷卻水孔深度加深,由距模具表面20 mm變成12 mm,以此快速帶走附近模具熱量,降低模溫;將所有模具冷卻水管與水管統一編號,一一對應,防止模具保全時裝錯,影響冷卻效果[5,6]。②降低澆注溫度,由675℃變為645℃。③延長縮孔處模具噴涂時間,由2 s變成3 s。實施上述整改措施后,縮孔區域模具噴涂后溫度大幅度降低,約為200℃,屬于正常范圍。縮孔率有4.8%降低到4%,說明此類措施對縮孔具有一定效果,但不能徹底解決此區域的縮孔問題。后期分析及對策:通過前面兩次改善,基本保證壓鑄模具處于理論上的合理狀態,即澆注系統設計合理、冷卻系統布置合適,工藝參數設計*優。然而,鑄件縮孔率仍有4%之多。鑄件縮孔處壁厚為22.6 mm,遠大于其他部位的壁厚,較大的壁厚可能引起鑄件中心凝固時補縮不足,增壓結束后此區域還沒有完全凝固,繼續收縮產生縮孔[7~10],模流分析見圖4。因此,如何解決鑄件縮孔處的補縮不足,也許才是問題的關鍵。一般來講,鑄件的補縮時通過料餅→澆道→內澆口→鑄件這條路徑進行的。由于鑄件厚大部位后于內澆口凝固,切斷了增壓后期的補縮通道,因此無法補縮。
縮孔是鋁合金壓鑄件常見的內部缺陷,常出現在產品壁厚較大或者易形成熱點的位置。一般來講,只要縮孔不影響產品的使用性能,都以合格的方式來判定。然而,對于一些重要部位,如汽車發動機汽缸體的冷卻水道孔或潤滑油道孔,出現縮孔是不允許判定合格的。
某企業的一款鋁合金制發動機曲軸箱,采用布勒28000kN冷室壓鑄機鑄造,材質為ADC12合金,成分見表1。鑄件毛坯質量為6.3 kg,后工序進行X射線探傷時發現第二個曲軸軸承孔油道出現縮孔,離油道約8 mm,存在較大的漏油風險。據統計,2017年該位置的縮孔報廢率為5%,經過一系列的探索,成功地將廢品率降低為0.2%。本課題從鋁合金壓鑄件縮孔的形成機理[1-5]和鑄造條件兩方面出發,分析鑄件產生縮孔的原因,尋求改善措施,以期為日后解決鋁合金壓鑄件縮孔問題提供參考。一、鋁合金壓鑄件縮孔形成機理及形態--縮孔形成機理:導致鋁合金壓鑄件縮孔的原因較多,追溯其本源,主要是鋁合金從液相向固相轉變過程中鋁液補縮不足而導致。常見的縮孔原因有:①模溫梯度不合理,導致鋁液局部收縮不一致。②鋁液澆注量偏少,導致料餅薄,增壓階段補壓不足。③模具存在熱結或尖銳區域。④模具的內澆口寬度不夠,面積較小,導致鑄件過早凝固,增壓階段壓力傳遞受阻、鋁液無法補縮。⑤鑄造壓力設置過低,補縮效果較差。圖1為鋁合金鑄件縮孔形成的示意圖。鑄件縮孔形態:縮孔是一種鋁合金壓鑄件乃至鑄件常見的內部缺陷,常出現在產品壁厚較大、模具尖角和模溫溫差較大等區域。圖2為某款發動機曲軸箱縮孔形態,縮孔呈似橢圓狀,距離軸承油道孔約10 mm,內壁粗糙,無光澤。縮孔區域鑄件壁厚較大,約為22 mm;油道孔銷子前端無冷卻水,模溫較高。汽車發動機曲軸的兩大軸頸(主軸頸和連桿軸頸)工作載荷較大,磨損嚴重,工作時必須進行壓力潤滑。在此情況下,軸頸的油道孔附近若存在縮孔,將會嚴重影響潤滑效果。二、縮孔相關對策:鋁合金壓鑄件產生鑄造缺陷的原因有產品本身的結構特征、模具設計得澆注系統及冷卻系統設計不合理、工藝參數設計不合理等原因[1~4]。根據常見的鑄造缺陷原因以及鋁合金鑄件缺陷處理流程,探索解決鋁合金壓鑄件厚大部位縮孔的相應對策。前期分析及對策:鑄件縮孔的前期分析從容易操作的工藝參數出發,通過現場測量及觀察,測得模具內澆口厚度為4 mm,計算的內澆口速度為40 m/s,產品壁厚*薄處為4.6 mm;料餅厚度為25 mm;鑄造壓力為60MPa。由經驗可知,模具設計符合產品的結構特征,模具澆注系統應該不存在增壓階段補縮不足的問題。但是,增壓階段的鋁液補縮與料餅厚度和增壓壓力有直接的關系,合適的料餅厚度與鑄造壓力才能形成內部組 織致密的鑄件,因此,可以懷疑縮孔是由鑄造壓力偏低和料餅偏薄而導致的。前期鑄件縮孔的對策分為兩個:①鑄造壓力由之前的65MPa提高至90MPa;②料餅厚度有原來的25 mm調整為30 mm。采用上述措施后,經過小批量專流驗證,縮孔率由5%減低為4.8%,效果不明顯,說明工藝參數不是引起鑄件縮孔的主因。中期分析及對策:由于引起鑄件縮孔的本質原因是鋁液凝固時補縮不足而導致,而模具溫度分布不均容易導致鋁液凝固順序不合理,從而補縮不足,因此,中期對策分析主要從確保合理的模具溫度入手。由產品3D模型可知,鑄件縮孔處壁厚為22.6mm,壁厚較大,容易引起較高的模具溫度。鋁液凝固時,壁厚較大鑄件內部鋁液由于溫度較高,尚處于液相或者固液混合相,而此時內澆口進行補縮的通道可能已經凝固。這樣,在增壓階段鑄件無法進行鋁液補縮,從而有形成縮孔的可能。為確保合適的模具溫度,采用熱成像儀測得脫模劑噴涂后模具*高溫度為272℃(見圖3),高于正常的模具噴涂后溫度,其他區域模具溫度及其分布整體正常。因此,需要降低縮孔處模溫。另外,測得此處冷卻水孔底部距離模具型腔表面距離較大為20 mm,因為較大的熱傳遞距離會降低模具的冷卻效果,所以需要對冷卻水孔進行更改。為降低縮孔處模具溫度,主要采取3個方法:①改善模具冷卻系統。將縮孔附件的冷卻水孔深度加深,由距模具表面20 mm變成12 mm,以此快速帶走附近模具熱量,降低模溫;將所有模具冷卻水管與水管統一編號,一一對應,防止模具保全時裝錯,影響冷卻效果[5,6]。②降低澆注溫度,由675℃變為645℃。③延長縮孔處模具噴涂時間,由2 s變成3 s。實施上述整改措施后,縮孔區域模具噴涂后溫度大幅度降低,約為200℃,屬于正常范圍。縮孔率有4.8%降低到4%,說明此類措施對縮孔具有一定效果,但不能徹底解決此區域的縮孔問題。后期分析及對策:通過前面兩次改善,基本保證壓鑄模具處于理論上的合理狀態,即澆注系統設計合理、冷卻系統布置合適,工藝參數設計*優。然而,鑄件縮孔率仍有4%之多。鑄件縮孔處壁厚為22.6 mm,遠大于其他部位的壁厚,較大的壁厚可能引起鑄件中心凝固時補縮不足,增壓結束后此區域還沒有完全凝固,繼續收縮產生縮孔[7~10],模流分析見圖4。因此,如何解決鑄件縮孔處的補縮不足,也許才是問題的關鍵。一般來講,鑄件的補縮時通過料餅→澆道→內澆口→鑄件這條路徑進行的。由于鑄件厚大部位后于內澆口凝固,切斷了增壓后期的補縮通道,因此無法補縮。
雜質元素的影響-釩在鋁合金中構成VAl11難熔化合物,在熔鑄進程中起細化晶粒效果,但比鈦和鋯的效果小。釩也有細化再結晶安排、進步再結晶溫度的效果。鈣在鋁合金中固溶度極低,與鋁構成CaAl4化合物,鈣又是鋁合金的超塑性元素,大概5%鈣和5%錳的鋁合金具有超塑性。鈣和硅構成CaSi,不溶于鋁,因為減小了硅的固溶量,可略進步工業純鋁的導電功能。鈣能改進鋁合金切削功能。CaSi2不能使鋁合金熱處理強化。量鈣有利于去掉鋁液中的氫。鉛、錫、鉍元素是低熔點金屬,它們在鋁中固溶度不大,略下降合金強度,但能改進切削功能。鉍在凝結進程中脹大,對補縮有利。高鎂合金中參加鉍可避免鈉脆。銻首要用作鍛造鋁合金中的蛻變劑,變形鋁合金很少運用。僅在Al-Mg變形鋁合金中替代鉍避免鈉脆。銻元素參加某些Al-Zn-Mg-Cu系合金中,改進熱壓與冷壓工藝功能。鈹在變形鋁合金中可改進氧化膜的構造,削減熔鑄時的燒損和攙雜。鈹是有毒元素,能使人發生過敏性中毒。因而,觸摸食物和飲料的鋁合金中不能富含鈹。焊接資猜中的鈹含量一般操控在8μg/ml以下。用作焊接基體的鋁合金也應操控鈹的含量。鈉在鋁中幾乎不溶解,較大固溶度小于0.0025%,鈉的熔點低(97.8℃),合金中存在鈉時,在凝結進程中吸附在枝晶外表或晶界,熱加工時,晶界上的鈉構成液態吸附層,發生脆性開裂時,構成NaAlSi化合物,無游離鈉存在,不發生“鈉脆”。當鎂含量超2%時,鎂攫取硅,分出游離鈉,發生“鈉脆”。因此高鎂鋁合金不允許運用鈉鹽熔劑。避免“鈉脆”的辦法有氯化法,使鈉構成NaCl排入渣中,加鉍使之生成Na2Bi進入金屬基體;加銻生成Na3Sb或加入稀土亦可起到一樣的效果。
鋁合金零件表面變黑的原因:鋁氧化加工鋁合金鑄造一般都是用金屬型鑄造,金屬鋁及鋁合金具有很好的流動性和可塑性,但在使用過程中容易變黑,原因為:(1)工藝設計不合理。鋁合金壓鑄件在清洗或壓檢后處理不當,為鋁合金壓鑄件發霉變黑創造了條件,加速了霉變的生成。(2)倉儲管理不到位。將鋁合金壓鑄件存放在倉庫不同的高度,其發霉的狀況也不同。(3)鋁合金的內部因素。很多鋁合金壓鑄件廠家在壓鑄、機加工工序之后,不做任何清潔處理,或者簡單的用水沖沖,無法做到徹底清洗干凈,壓鑄鋁表面殘留有脫模劑、切削液、皂化液等腐蝕性物質以及其他污漬,這些污漬加快了鋁合金壓鑄件長霉點變黑的速度。(4)鋁合金外部環境因素。鋁是活潑金屬,在一定的溫度和濕度條件下極易氧化變黑或發霉,這是鋁本身的特性決定的。(5)選用清洗劑不得當。選用的清洗劑具有強腐蝕性,造成壓鑄鋁腐蝕氧化。
鋁合金零件表面變黑的原因:鋁氧化加工鋁合金鑄造一般都是用金屬型鑄造,金屬鋁及鋁合金具有很好的流動性和可塑性,但在使用過程中容易變黑,原因為:(1)工藝設計不合理。鋁合金壓鑄件在清洗或壓檢后處理不當,為鋁合金壓鑄件發霉變黑創造了條件,加速了霉變的生成。(2)倉儲管理不到位。將鋁合金壓鑄件存放在倉庫不同的高度,其發霉的狀況也不同。(3)鋁合金的內部因素。很多鋁合金壓鑄件廠家在壓鑄、機加工工序之后,不做任何清潔處理,或者簡單的用水沖沖,無法做到徹底清洗干凈,壓鑄鋁表面殘留有脫模劑、切削液、皂化液等腐蝕性物質以及其他污漬,這些污漬加快了鋁合金壓鑄件長霉點變黑的速度。(4)鋁合金外部環境因素。鋁是活潑金屬,在一定的溫度和濕度條件下極易氧化變黑或發霉,這是鋁本身的特性決定的。(5)選用清洗劑不得當。選用的清洗劑具有強腐蝕性,造成壓鑄鋁腐蝕氧化。
在湖南省湘潭市采買鋁合金型材,精密管來圖加工定制到恒永興金屬材料銷售
有限公司,無論您是個人用戶還是企業采購,我們都將竭誠為您服務。品質保證,價格優惠,廠家直銷,歡迎有需要的客戶來電。聯系人:李經理-18802286588,QQ:554918566,地址:《北辰區雙街鎮京津路西(北方實業發展有限公司內)》。