隨著生鐵價格的提高鑄鐵型材生產成本不斷增加。為降低生產成本本課題在HT250材質的基礎上采用氮、鈦、鈮對鐵液進行合金化通過金相組織觀察、SEM分析、EDS分析、拉伸試驗和硬度試驗研究了氮、鈦、鈮對灰鑄鐵組織及性能的影響規律。 試驗結果表明含氮量為0.0055%~0.013%、含錳量為1.0%-1.36%時試樣的金相組織為A型石墨+細片狀珠光體+少量鐵素體。 鑄鐵型材在重工業中需求量大,被廣泛應用于交通運輸、機床、印刷、農業機械等支柱行業。對鼓肚缺陷,在鑄鐵型材的水平連鑄過程中采用反弧度法工藝,使鑄鐵型材在結晶器的停留時間過長,導致在扁平方向上鑄鐵型材頂部略微向下凹,當拉拔參數調整合適時,下凹及鼓肚現象基本消失。反弧度法工藝制各的鑄鐵型材組織更為均勻,力學性能更為優良。與實施反弧度法之前的鑄鐵型材相比,實施反弧度法之后的鑄鐵型材硬度得到提高,組織更為均勻,并且其抗拉強度指標高于鑄鐵型材標準(JBT10854-2008水平連續鑄造鑄鐵型材) 性能要求。同時,伸長率指標均超過LZQT500-7規定的指標。與拉伸性能結果類似,反弧度法試樣的抗壓強度高于未實施反弧度法試樣的抗拉強度。在適當含氮量(0.0080%左右)基礎上含鈦量在0.055%-0.149%范圍內時試樣的金相組織為A型和D型石墨+珠光體+少量鐵素體。隨著含鈦量的增加:A型石墨減少D型石墨增多;鐵素體的含量增多珠光體的含量減少。 試樣的抗拉強度呈現降低的趨勢當含鈦量為0.149%時試樣的抗拉強度小為230MPa;而試樣的布氏硬度略有增加當含鈦量為0.149%時試樣的布氏硬度大為219HBW。鈦在含氮灰鑄鐵中的存在形式有以下兩種:少部分固溶于基體中呈均勻分布;大部分與鐵液中的碳、氮形成鈦的碳氮化物并多以三角形、四邊形及帶棱角的不規則塊狀鑲嵌于基體之中呈彌散分布。
江西高硅QT420-12球鐵棒零賣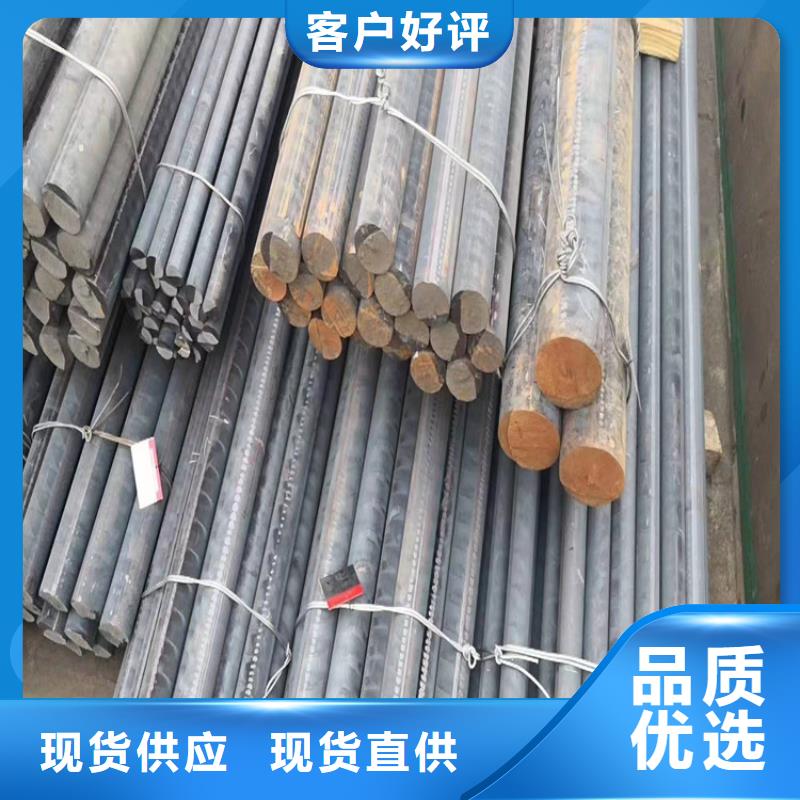
當前汽車發動機鑄鐵型材斷軸缺陷的研究主要采用“傳統實驗試錯法”,耗時耗材、難以快速有效獲得砂芯質量調控策略。為此,本文分析從砂芯制作到澆注全流程多工序相關參數與斷軸的關系,確定造成斷軸缺陷的主要因子;采用“BP神經網絡法”建立一套汽車發動機鑄鐵型材斷軸缺陷的診斷模型,并基于此模型研究各項影響因子對缺陷產生的敏感程度;結合實際過程相關參數的波動性獲得過程控制策略,用以指導實際生產。對出現在鑄鐵型材內部的夾雜缺陷,進行了地研究分析,明確了夾雜物的分布規律、元素組成、來源及形成原因,并就如何控制該缺陷的產生給出了相關的建議。對大斷面型材表面出現的疤皮缺陷,分析了形成原因,討論了影響其形成的因素,并提出了能有效疤皮缺陷的措施。優化設計后得到的鑄鐵型材新生產線,能夠滿足 尺寸為400mm的鑄鐵型材的生產,且生產鑄鐵型材的工序簡化,其中大尺寸的夾雜物主要來源于球化和孕育處理,因此解決鑄鐵型材內部夾雜問題的關鍵是控制球化和孕育處理的相關參數.對于鑄鐵型材表面存在的疤皮缺陷,生產實踐證明,采取提高鐵水溫度、保證鐵水純凈度、適當提高拉拔速度、改進爐膛底部結構及阻斷結晶器兩段石墨套間橫向傳熱的舉措能夠有效地。首先分析了汽車發動機鑄鐵型材的生產工藝質量狀況,系統闡述了常見的缺陷問題,然后對斷軸缺陷的研究現狀進行了深入調研,并結合企業實際生產分析了砂芯制作與應用的全流程工序,確定了造成斷軸缺陷的主要因子。同時結合企業ERP系統,對斷軸缺陷的主要影響因子數據進行挖掘,并以典型鑄鐵型材為例詳細闡述了數據挖掘過程.
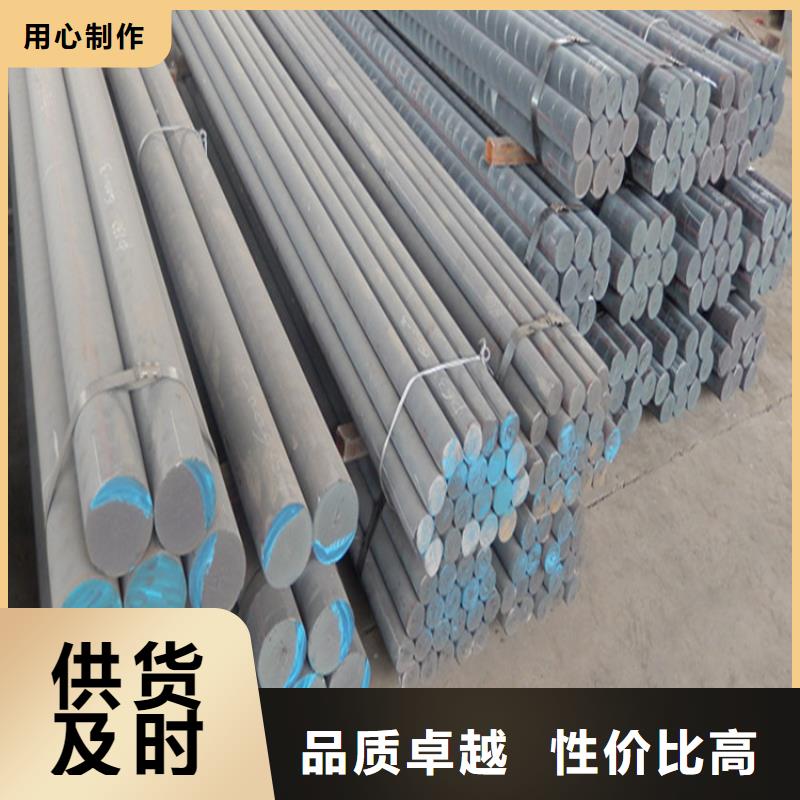
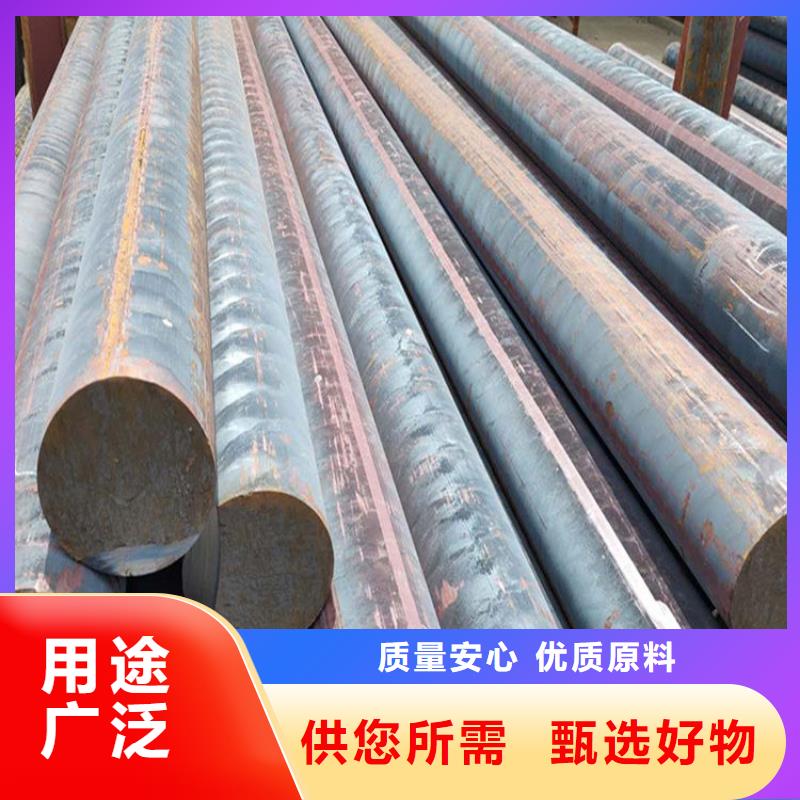