


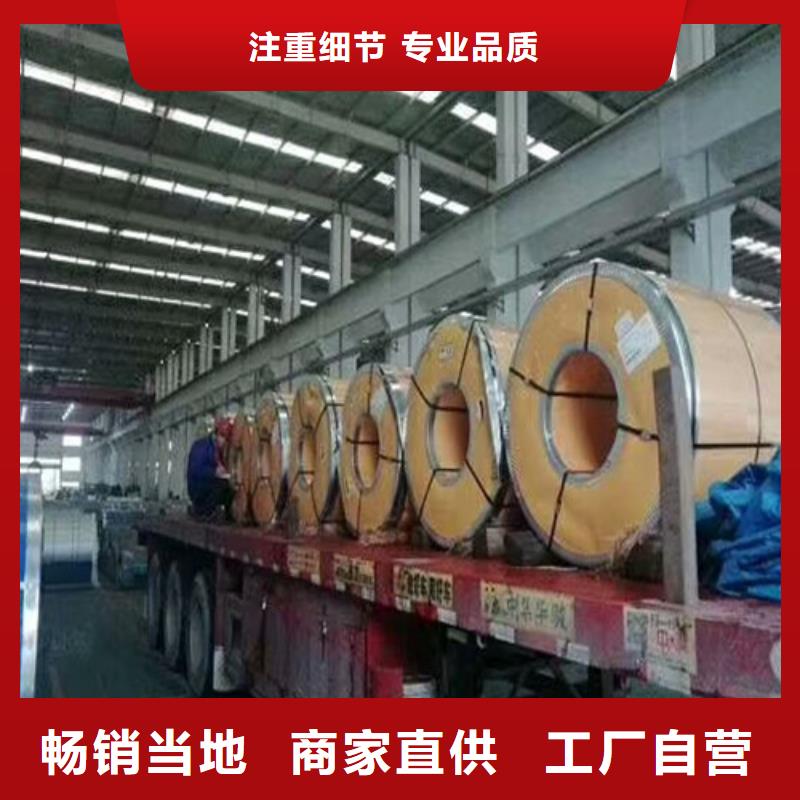
恩施00Cr18Ni14Mo2Cu2系在00Cr17Ni14Mo2基礎上加入約2%Cu而發展起來的, 在稀硫酸、磷酸等還原性酸中以及在醋酸、甲酸等有機酸中,其耐蝕性優于恩施00Cr17NI14Mo2和00Cr19Ni13Mo3。此鋼系耐稀硫酸腐蝕的較好材料,在室溫、中等濃度的硫酸中耐蝕性亦佳。它是制造化工、化肥、化纖設備的重要耐蝕材料,可用作焊接結構件和管道、容器等。
此鋼種與00Cr18Ni14Mo2Cu2鋼相比,由于碳含量高且加入碳化物形成元素Ti,在具有較高強度的同時,其耐晶間腐蝕性能良好。加之此鋼鎳含量高,組織更加穩定,不存在鐵素體,熱塑性好,因而較00Cr18Ni14Mo2Cu2更適于生產不銹鋼管材。此鋼的耐蝕性在硫酸等還原性介質中要較恩施00Cr18Ni14Mo2Cu2鋼為優。由于它在磷酸、中溫中等濃度硫酸中耐蝕性優良,故多用于制造酸洗、合成橡膠、人造絲浸槽等與硫酸相接觸的設備。
70年代以來,我國不銹鋼材料研究工作的其它重要進展有:研制了恩施高強度和超高強度的恩施馬氏體時效不銹鋼并投入工業試制與應用;采用真空感應爐、真空電子束爐和真空自耗爐冶煉并批量生產了C+N≤150-250ppm的高純鐵素體恩施不銹鋼00Cr18Mo2、00Cr26Mo1和00Cr30Mo2;含Mo量≥4.5%的高Mo和高Mo含N的Cr-Ni奧氏體不銹鋼,例如研制成功00Cr20Ni25Mo4.5Cu、00Cr18Ni18Mo5(N)、00Cr25Ni25Mo5N等并在化工、石化和海洋開發中獲得了應用;在解決濃硝酸腐蝕和固溶態晶間腐蝕方面,研制了00Cr25Ni20Nb和幾種超低碳高硅不銹鋼,80年代以來,超低碳并對鋼中磷含量和α相量嚴加控制的尿素級恩施不銹鋼00Cr18Ni14Mo2和00Cr25Ni22Mo2N兩種牌號研制完成,它們的板、管、棒材、鍛件以及焊接材料均在大中型尿素工業中得到了應用,取得了滿意的結果;由于一些特殊鋼廠陸續建成冶煉不銹鋼的爐外精煉設備,例如AOD(氬氧精煉爐)、VOD(真空氧精煉爐)等并已投產,我國不銹鋼的冶煉技術上了一個新臺階。它不僅使低碳、超低碳不銹鋼的生產變得輕而易舉,而且使不銹鋼的內在質量提高,成本降低。由于含Ti的18-8型Cr-Ni奧氏體鋼存在一系列缺點,美、日等工業先進 早在60年代便已經實現了由含Ti不銹鋼到普遍采用低碳、超低碳不銹鋼的過渡,而我國是在1985—1990年間才大力進行低碳、超低碳不銹鋼的開發、生產與應用,取得了一些可喜的進展,例如1988年底我國低碳、超低碳18-8型不銹鋼產量已占我國不銹鋼產量的10%左右。但與不銹鋼板生產、應用的先進 相比(例如日、美等國含Ti的18-8型Cr-Ni鋼僅占不銹鋼產量的1.5%左右),還存在著很大的差距。80年代,我國還開展了控氮(N 0.05%—0.10%)和氮合金化(N>0.10%)Cr-Ni奧氏體不銹鋼的研制工作。試驗表明,氮在Cr-Ni奧氏體不銹鋼和雙相不銹鋼中是一種無價且非常有益的合金元素。對氮的強化作用,降低鋼的晶間腐蝕敏感性,改善鋼的耐蝕性,特別是改善鋼的耐點蝕等方面的機制,正在進行深入的研究工作。幾種控氮和氮合金化的Cr-Ni奧氏體不銹鋼已結合工程需要投入了批量生產和應用。
恩施1Cr18Ni12Mo3Ti恩施0Cr18Ni12Mo3Ti和恩施00Cr19Ni13Mo3這四種含氮奧氏體不銹鋼均是在其各自的不含氮鋼種的基礎上發展起來的。它們既保留了原來各相應不含氮鋼種的耐蝕性特點,同時由于氮的強化作用提高了強度和加工硬化傾向,而塑性、韌性仍然維持很高的水平。另外,氮的加入也進一步改善在某些方面的耐蝕性,特別是耐點腐蝕、縫隙腐蝕和晶間腐蝕性能。這些鋼可用在各相應不含氮鋼的應用場合,同時可承受更重的負荷,因而可減少材料消耗。從實用角度上講,目前重要的是0Cr19Ni9N和00Cr17Ni13Mo2N兩種。0Cr19Ni9N鋼主要用于要求一定耐蝕性和較高強度或減輕重量的設備及構件,比如飛機和宇航器中的部件與裝置,海水設備中泵、閥以及船舶的軸與推進器等。00Cr17Ni13Mo2N鋼主要用于化工、化肥(特別是尿素生產)裝置中的高壓設備和管線,如合成塔、反應器和容器有關設備。
恩施不銹鋼的發展和現狀
我國用電弧爐大量生產不銹鋼系在1949年以后,早期先生產Cr13型馬氏體不銹鋼,掌握生產技術后,大量生產恩施18-8型Cr-Ni奧氏體鋼,例如1Cr18Ni9Ti,則始于1952年。隨后,為適應國內化學工業發展的需要,又開始生產含Mo2%-3%的1Cr18Ni12Mo2Ti和1Cr18Ni12Mo3Ti等。為了節約貴重元素鎳,自1959年起開始仿制以MnN代Ni的1Cr17Mn6Ni5N和1Cr18Mn8Ni5N1958年向AISI 204鋼中加入Mo2%-3%,研制了1Cr18Mn10Ni5Mo3N(204+Mo)用于全循環法尿素生產裝置以代替1Cr18Ni12Mo2Ti。50年代末到60年代初,開始工業試制恩施1Cr17Ti,1Cr17Mo2Ti和1Cr25Mo3Ti等無鎳鐵素體不銹鋼,并開始研究耐發煙硝酸腐蝕的高硅不銹鋼1Cr17Ni14Si4ALTi(相當于蘇聯牌號ЭИ654),此鋼種實際上是一種α+γ雙相不銹鋼。60年代開始,由于國內化工、航天、航空、原子能等工業發展的需要以及采用電爐氧氣煉鋼技術,一大批新鋼種,如17-4PH,17-7PH,PH15-7Mo等沉淀硬化不銹鋼,含C≤0.03%的超低碳不銹鋼00Cr18Ni10、00Cr18Ni14Mo2、00Cr18Ni14Mo3以及無Ni的Cr-Mn-N不銹鋼1Cr18Mn14Mo2N(A4)相繼研制成功并投入了生產。70年代起,為解決化工、原子能工業中所出現的18-8型Cr-Ni鋼的氯化物應力腐蝕問題,一些α+γCr-Ni雙相不銹鋼相繼研制完成并正式生產和應用,主要鋼號有1Cr21Ni5Ti,00Cr26Ni6Ti,00Cr26Ni7Mo2Ti,00Cr18Ni5Mo3Si2(3RE60)和00Cr18Ni6Mo3Si2Nb等。00Cr18Ni6Mo3Si2Nb是為了解決瑞典牌號3RE60焊后易出現單相鐵素體組織,導致耐蝕性和韌性下降而發展的含N、Nb的α+γ雙相不銹鋼。到80年代,為解決氯化物的點蝕、縫隙腐蝕等局部腐蝕破壞又研制和仿制了含N的第二代α+γ雙相不銹鋼,如00Cr22Ni5Mo2N00Cr25Ni6Mo3N和00Cr25Ni7Mo3WCuN等,不僅使我國的雙相不銹鋼形成了系列,而且還深入研究了它們的組織和性能以及N在雙相不銹鋼中的作用機制。