當前位置:
天津 恒永興金屬材料銷售
有限公司 >益陽當地行業新聞
【鋁合金型材,流體管滿足客戶需求】
更新時間:2025-02-11 22:54:58 瀏覽次數:2 公司名稱:天津 恒永興金屬材料銷售 有限公司
以下是:【鋁合金型材,流體管滿足客戶需求】的產品參數
產品參數 | |
---|---|
產品價格 | 89 |
發貨期限 | 電議 |
供貨總量 | 電議 |
運費說明 | 電議 |
品牌 | 恒永興 |
規格 | 齊全 |
價格 | 電議 |
以下是:【鋁合金型材,流體管滿足客戶需求】的圖文視頻
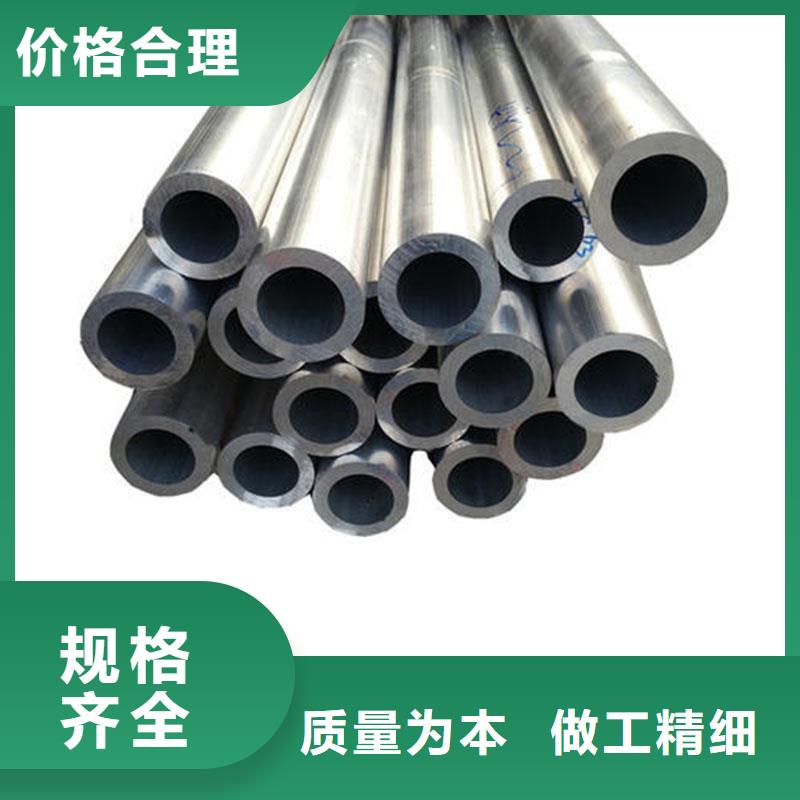

【鋁合金型材,流體管滿足客戶需求】,恒永興金屬材料銷售
有限公司專業從事【鋁合金型材,流體管滿足客戶需求】,聯系人:李經理,電話:022-86869388、18802286588,QQ:554918566,發貨地:天津北辰區雙街鎮京津路西(北方實業發展有限公司內)發貨到湖南省 益陽市 赫山區、南縣、桃江縣、安化縣、沅江市,以下是【鋁合金型材,流體管滿足客戶需求】的詳細頁面。 湖南省,益陽市 益陽市是“中國羽毛球運動之鄉”“中國竹子之鄉”“中國黑茶之鄉”“中國淡水漁都”“花鼓戲窩子”,先后獲得省級園林城市、中國杰出綠色生態城市、森林城市、衛生城市、全國文明城市提名城市、湖南省歷史文化名城等稱號,自古是江南富饒的“魚米之鄉”。
想要了解【鋁合金型材,流體管滿足客戶需求】產品的魅力?視頻為你揭曉答案!
以下是:【鋁合金型材,流體管滿足客戶需求】的圖文介紹
鋁及鋁合金焊絲的選擇主要根據母材的種類,對接頭抗裂性能、力學性能及耐蝕性等方面的要求綜合考慮。有時當某項成為主要矛盾時,則選擇焊絲就著重從解決這個主要矛盾入手,兼顧其它方面要求。一般情況下,焊接鋁及鋁合金都采用與母材成分相同或相近牌號的焊絲,這樣可以獲得較好的耐蝕性;但焊接熱裂傾向大的熱處理強化鋁合金時,選擇焊絲主要從解決抗裂性入手,這時焊絲的成分與母材的差別就很大。
常見缺陷(焊接問題)及防止措施1、燒穿---產生原因:a、熱輸入量過大;b、坡口加工不當,焊件裝配間隙過大;c、點固焊時焊點間距過大,焊接過程中產生較大的變形量。防止措施:a、適當減小焊接電流、電弧電壓,提高焊接速度;b、大鈍邊尺寸,減小根部間隙;c、適當減小點固焊時焊點間距。2、氣孔---產生原因:a、母材或焊絲上有油、銹、污、垢等;b、焊接場地空氣流動大,不利于氣體保護;c、焊接電弧過長,降低氣體保護效果;d、噴嘴與工件距離過大,氣體保護效果降低;e、焊接參數選擇不當;f、重復起弧處產生氣孔;g、保護氣體純度低,氣體保護效果差;h、周圍環境空氣濕度大。防止措施:a、焊前仔細清理焊絲、焊件表面的油、污、銹、垢和氧化膜,采用含脫氧劑較高的焊絲;b、合理選擇焊接場所;c、適當減小電弧長度;d、保持噴嘴與焊件之間的合理距離范圍;e、盡量選擇較粗的焊絲,同時增加工件坡口的鈍邊厚度,一方面可以允許使用大電流,公眾號:焊王,另一方面也使焊縫金屬中焊絲比例下降,這對降低氣孔率是行之有效的;f、盡量不要在同一部位重復起弧,需要重復起弧時要對起弧處進行打磨或刮除;一道焊縫一旦起弧要盡量焊長些,不要隨意斷弧,以減少接頭量,在接頭處需要有一定焊縫重疊區;g、換保護氣體;h、檢查氣流大小;i、預熱母材;j、檢查是否有漏氣現象和氣管損壞現象;k、在空氣濕度較低時焊接,或采用加熱系統。3、電弧不穩---產生原因:電源線連接、污物或者有風。防止措施:a、檢查所有導電部分并使表面保持清潔;b、將接頭處的臟物掉;c、盡量不要在能引起氣流紊亂的地方進行焊接。4、焊縫成型差---產生原因:a、焊接規范選擇不當;b、焊槍角度不正確;c、焊工操作不熟練;d、導電嘴孔徑太大;e、焊絲、焊件及保護氣體中含有水分。防止措施:a、反復調試選擇合適的焊接規范;b、保持合適的焊槍傾角;c、選擇合適的導電嘴孔徑;d、焊前仔細清理焊絲、焊件,保證氣體的純度。5、未焊透---產生原因:a、焊接速度過快,電弧過長;b、坡口加工不當,裝備間隙過小;c、焊接規范過小;d、焊接電流不穩定。防止措施:a、適當減慢焊接速度,壓低電弧;b、適當減小鈍邊或增加根部間隙;c、增加焊接電流及電弧電壓,保證母材足夠的熱輸入能量;d、增加穩壓電源裝置e、細焊絲有助于提高熔深,粗焊絲提高熔敷量,應酌情選擇。6、未熔合---產生原因:a、焊接部位氧化膜或銹跡未干凈;b、熱輸入不足。防止措施:a、焊前清理待焊處表面b、提高焊接電流、電弧電壓,減小焊接速度;c、對于厚板采用U型接頭,而一般不采用V型接頭。7、裂紋---產生原因:a、結構設計不合理,焊縫過于集中,造成焊接接頭拘束應力過大b、熔池過大、過熱、合金元素燒損多;c、焊縫末端的弧坑冷卻快;d、焊絲成分與母材不匹配;e、焊縫深寬比過大。防止措施:a、正確設計焊接結構,合理布置焊縫,使焊縫盡量避開應力集中區,合理選擇焊接順序;b、減小焊接電流或適當增加焊接速度;c、收弧操作要正確,加入引弧板或采用電流衰減裝置填滿弧坑;d、正確選用焊絲。8、夾渣---產生原因:a、焊前清理不徹底;b、焊接電流過大,導致導電嘴局部熔化混入熔池而形成夾渣c、焊接速度過快。防止措施:a、加強焊前清理工作,多道焊時,每焊完一道同樣要進行焊縫清理;b、在保證熔透的情況下,適當減小焊接電流,大電流焊接時導電嘴不要壓太低;c、適當降低焊接速度,采用含脫氧劑較高的焊絲,提高電弧電壓。9、咬邊---產生原因:a、焊接電流太大,焊接電壓太高;b、焊接速度過快,填絲太少;c、焊槍擺動不均勻。防止措施:a、適當的調整焊接電流和電弧電壓;b、適當增加送絲速度或降低焊接速度;c、力求焊槍擺動均勻。10、焊縫污染---產生原因:a、不適當的保護氣體覆蓋;b、焊絲不潔;c、母材不潔。防止措施:a、檢查送氣軟管是否有泄漏情況,是否有抽風,氣嘴是否松動,保護氣體使用是否正確;b、是否正確的儲存焊接材料;c、在使用其它的機械清理前,先將油和油脂類物質掉;d、在使用不銹鋼刷之前將氧化物掉。11、送絲性不良---產生原因:A、導電嘴與焊絲打火;b、焊絲磨損、噴弧;d、送絲軟管太長或太緊;e、送絲輪不適當或磨損;f、焊接材料表面毛刺、劃傷、灰塵和污物較多。防止措施:a、降低送絲輪張力,使用慢啟動系統;b、檢查所有焊絲接觸表面情況并盡量減少金屬與金屬的接觸面;c、檢查導電嘴情況及送絲軟管情況,檢查送絲輪狀況;d、檢查導電嘴的直徑大小是否匹配;e、使用耐磨材料以避免送絲過程中發生截斷情況;f、檢查焊絲盤磨損狀況;g、選擇合適的送絲輪尺寸,形狀及合適的表面情況;h、選擇表面質量較好的焊接材料。12、起弧不良---產生原因:a、接地不良;b、導電嘴尺寸不對;c、沒有保護氣體。防止措施:a、檢查所有接地情況是否良好,使用慢啟動或熱起弧方式以方便起弧;b、檢查導電嘴內空是否被金屬材料堵塞;c、使用氣體預清理功能;d、改變焊接參數。
常見缺陷(焊接問題)及防止措施1、燒穿---產生原因:a、熱輸入量過大;b、坡口加工不當,焊件裝配間隙過大;c、點固焊時焊點間距過大,焊接過程中產生較大的變形量。防止措施:a、適當減小焊接電流、電弧電壓,提高焊接速度;b、大鈍邊尺寸,減小根部間隙;c、適當減小點固焊時焊點間距。2、氣孔---產生原因:a、母材或焊絲上有油、銹、污、垢等;b、焊接場地空氣流動大,不利于氣體保護;c、焊接電弧過長,降低氣體保護效果;d、噴嘴與工件距離過大,氣體保護效果降低;e、焊接參數選擇不當;f、重復起弧處產生氣孔;g、保護氣體純度低,氣體保護效果差;h、周圍環境空氣濕度大。防止措施:a、焊前仔細清理焊絲、焊件表面的油、污、銹、垢和氧化膜,采用含脫氧劑較高的焊絲;b、合理選擇焊接場所;c、適當減小電弧長度;d、保持噴嘴與焊件之間的合理距離范圍;e、盡量選擇較粗的焊絲,同時增加工件坡口的鈍邊厚度,一方面可以允許使用大電流,公眾號:焊王,另一方面也使焊縫金屬中焊絲比例下降,這對降低氣孔率是行之有效的;f、盡量不要在同一部位重復起弧,需要重復起弧時要對起弧處進行打磨或刮除;一道焊縫一旦起弧要盡量焊長些,不要隨意斷弧,以減少接頭量,在接頭處需要有一定焊縫重疊區;g、換保護氣體;h、檢查氣流大小;i、預熱母材;j、檢查是否有漏氣現象和氣管損壞現象;k、在空氣濕度較低時焊接,或采用加熱系統。3、電弧不穩---產生原因:電源線連接、污物或者有風。防止措施:a、檢查所有導電部分并使表面保持清潔;b、將接頭處的臟物掉;c、盡量不要在能引起氣流紊亂的地方進行焊接。4、焊縫成型差---產生原因:a、焊接規范選擇不當;b、焊槍角度不正確;c、焊工操作不熟練;d、導電嘴孔徑太大;e、焊絲、焊件及保護氣體中含有水分。防止措施:a、反復調試選擇合適的焊接規范;b、保持合適的焊槍傾角;c、選擇合適的導電嘴孔徑;d、焊前仔細清理焊絲、焊件,保證氣體的純度。5、未焊透---產生原因:a、焊接速度過快,電弧過長;b、坡口加工不當,裝備間隙過小;c、焊接規范過小;d、焊接電流不穩定。防止措施:a、適當減慢焊接速度,壓低電弧;b、適當減小鈍邊或增加根部間隙;c、增加焊接電流及電弧電壓,保證母材足夠的熱輸入能量;d、增加穩壓電源裝置e、細焊絲有助于提高熔深,粗焊絲提高熔敷量,應酌情選擇。6、未熔合---產生原因:a、焊接部位氧化膜或銹跡未干凈;b、熱輸入不足。防止措施:a、焊前清理待焊處表面b、提高焊接電流、電弧電壓,減小焊接速度;c、對于厚板采用U型接頭,而一般不采用V型接頭。7、裂紋---產生原因:a、結構設計不合理,焊縫過于集中,造成焊接接頭拘束應力過大b、熔池過大、過熱、合金元素燒損多;c、焊縫末端的弧坑冷卻快;d、焊絲成分與母材不匹配;e、焊縫深寬比過大。防止措施:a、正確設計焊接結構,合理布置焊縫,使焊縫盡量避開應力集中區,合理選擇焊接順序;b、減小焊接電流或適當增加焊接速度;c、收弧操作要正確,加入引弧板或采用電流衰減裝置填滿弧坑;d、正確選用焊絲。8、夾渣---產生原因:a、焊前清理不徹底;b、焊接電流過大,導致導電嘴局部熔化混入熔池而形成夾渣c、焊接速度過快。防止措施:a、加強焊前清理工作,多道焊時,每焊完一道同樣要進行焊縫清理;b、在保證熔透的情況下,適當減小焊接電流,大電流焊接時導電嘴不要壓太低;c、適當降低焊接速度,采用含脫氧劑較高的焊絲,提高電弧電壓。9、咬邊---產生原因:a、焊接電流太大,焊接電壓太高;b、焊接速度過快,填絲太少;c、焊槍擺動不均勻。防止措施:a、適當的調整焊接電流和電弧電壓;b、適當增加送絲速度或降低焊接速度;c、力求焊槍擺動均勻。10、焊縫污染---產生原因:a、不適當的保護氣體覆蓋;b、焊絲不潔;c、母材不潔。防止措施:a、檢查送氣軟管是否有泄漏情況,是否有抽風,氣嘴是否松動,保護氣體使用是否正確;b、是否正確的儲存焊接材料;c、在使用其它的機械清理前,先將油和油脂類物質掉;d、在使用不銹鋼刷之前將氧化物掉。11、送絲性不良---產生原因:A、導電嘴與焊絲打火;b、焊絲磨損、噴弧;d、送絲軟管太長或太緊;e、送絲輪不適當或磨損;f、焊接材料表面毛刺、劃傷、灰塵和污物較多。防止措施:a、降低送絲輪張力,使用慢啟動系統;b、檢查所有焊絲接觸表面情況并盡量減少金屬與金屬的接觸面;c、檢查導電嘴情況及送絲軟管情況,檢查送絲輪狀況;d、檢查導電嘴的直徑大小是否匹配;e、使用耐磨材料以避免送絲過程中發生截斷情況;f、檢查焊絲盤磨損狀況;g、選擇合適的送絲輪尺寸,形狀及合適的表面情況;h、選擇表面質量較好的焊接材料。12、起弧不良---產生原因:a、接地不良;b、導電嘴尺寸不對;c、沒有保護氣體。防止措施:a、檢查所有接地情況是否良好,使用慢啟動或熱起弧方式以方便起弧;b、檢查導電嘴內空是否被金屬材料堵塞;c、使用氣體預清理功能;d、改變焊接參數。
6082合金:繼6N01合金普及以來,1972年成型的6082合金得到鐵路裝備制造部門的關注,此合金的強度介于7N01合金與6N01合金強度之間。6082-T5方形管的抗拉強度Rm(噴霧在線淬火)符合底架梁的相應要求。基礎實驗表明,此合金可以在相應領域實地應用。然而,若要在鐵路裝備部門廣泛推廣,仍需要做大量工作。對于30年前曾被視為萬無一失的鋁制列車的裝配節點的疲勞強度,由于列車載重條件改變和結構輕量化,已不適用于當前的新型高速列車,但是這與高寒地區的溫度無關,因為零下幾十攝氏度對鋁合金來說真是“小試鋒芒”,算不了什么低溫,同時溫度越低,鋁結構顯得越強韌。泡沫鋁:高速列車具有軸重輕、頻繁加減速和超載運行等特點,要求車體結構在滿足強度、剛度、、舒適的前提下盡可能輕量化。顯然,超輕泡沫鋁所具備的高比強、高比模、高阻尼等性能,與這些要求非常一致。國外對泡沫鋁在高速列車上的應用進行了詳細地研究與評估,發現填充泡沫鋁的鋼管吸能本領比空管的高35%~40%,抗彎強度提高40%~50%,從而可使車廂立柱和隔板更堅固,不易坍塌;用泡沫鋁填充機車頭部緩沖區,可提高吸收沖擊能的能力;用10mm厚泡沫鋁和薄鋁板制造的夾心板比原鋼板質量輕50%,而剛度卻提高了8倍。目前,中國高鐵有關單位正在研究用泡沫鋁夾心板制備高鐵車廂地板和車門的可行性。為加快解決下一代高鐵面臨的一系列重大科技問題,鐵道部門和中國科學院聯合成立了先進軌道交通力學研究中心,在對高速列車材料與結構可靠性、噪聲降低理論與技術等方面展開攻關研究,其中有相當一部分內容與超輕泡沫鋁有關。隨著高速列車運行速度的不斷,產生的噪聲對乘客乘坐舒適度與周邊環境的影響已成為高鐵發展的關鍵制約因素之一。相對于車內噪聲,車外噪聲對環境的影響更為嚴重,而高速列車通過隧道或兩列高鐵在隧道內交匯時產生的混響噪聲及由此產生的震動具有相當強的破壞力,如不有效控制,將可能成為高鐵的一大發展障礙。為了降低高速列車的噪聲污染,必須在經過人口密集區的鐵路兩側及隧道內設置屏障。超輕開孔泡沫鋁的主要功能之一是吸聲,而且該性能可通過改變孔型或聲結構調整。此外,泡沫鋁還具有良好的防腐、耐氣候和加工性能,因此是野外聲屏障的良好吸聲材料。
恒永興金屬材料銷售 有限公司成立以來,一直秉承“做好自己、做好 湖南益陽低中壓鍋爐管產品、同心同德共創美好生活 ”的經營理念,持續關注技術研發和制造技術,向社會提供創新優質 湖南益陽低中壓鍋爐管產品,為人類創造、便捷、舒適的生活。
淺談如何提高鋁型材用粉末涂料的耐候性:噴涂在鋁型材表面的粉末涂膜的耐候性,是影響鋁型材壽命的關鍵性因素。本文主要從粉末涂料的原材料、配方結構、制作工藝、固化條件等技術角度分析,并結合所做的實驗結果,總結出幾個提高粉末涂料耐候性的可供參考的思路,從而*終達到延長鋁型材壽命的目的。隨著國民經濟的快速發展,粉末涂料的戶外應用越來越普遍,人們對粉末涂層耐候性和耐久性的關注度不斷提高,特別是對鋁型材、天花板、幕墻板等室外用品表面的粉末涂膜的耐候性要求越來越高。粉末涂料主要由樹脂、固化劑、助劑、顏填料等組成,噴涂在鋁型材表面的涂層隨著時間的延長,受周圍自然因素如日曬、雨淋、氧化、冷熱變化以及生物等的作用,會出現性能逐漸降低的現象,即老化。粉末涂料抑制或延緩自然老化的能力稱為耐自然老化性,簡稱耐老化性,也叫耐候性。影響粉末涂料耐候性的因素很多,其中包括粉末涂料成分中的樹脂、固化劑、顏填料、助劑等各種原材料的性能、用量、配比等內部因素;以及粉末涂料制作過程的工藝條件和涂料的固化程度;還有涂膜的使用環境如日光(主要是紫外線)的作用、大氣的組成(氧、臭氧、工業煙霧等)、濕度(包括酸雨、鹽霧等)、溫度變化等外部因素。
從粉末涂料本身的角度來看,提高粉末涂層耐候性能主要從原材料、配方結構以及制作工藝等方面著手。一、原材料:粉末涂料主要由樹脂、固化劑、助劑、顏填料等材料組成,這些原材料的耐候性,基本上決定了涂料的耐候性。因此,要提高粉末涂料的耐候性能,首先要選擇耐候性能滿足鋁型材行業要求的原材料,而且這些耐候性合格的原材料也要滿足涂膜的其他性能。當涂膜的各項性能相互間產生沖突時,可以根據客戶的要求側重于某項性能,但是人工加速老化試驗結果要滿足GB 5237.4-2008中加速耐候性的要求。1.樹脂:因為樹脂是粉末涂料的主要成膜物質,是決定粉末涂料性質和涂膜性能的*主要成分,所以樹脂的選擇至關重要。選取市面上大型廠家常用的鋁型材用粉末涂料聚酯樹脂,使用同一配方結構和相同制作工藝分別制粉進行300小時耐老化試驗以及涂膜外觀比較,結果如表1所示。(加速老化條件為8小時光照,4小時凝露循環;UVB-313EL燈,輻照度0.65W/㎡,光照溫度60℃;凝露溫度50℃)由試驗結果可知,樹脂D、F、H在通一系列的樹脂中耐候性較好,但這種樹脂的缺點是分子量大,熔融黏度高,如果應用在平面粉中*終會導致涂膜流平性能差。所以,通過在粉末涂料配方中選用耐候性能好的樹脂來提高平面粉的耐候性能時,必須考慮到涂膜的流平是否會變差,變差之后客戶能否接受。2.固化劑:盡管HAA體系的固化劑環保型眾所周知,但是它的缺點是固化反應有副產物形成,厚噴時容易產生針孔、豬毛孔等弊端,涂膜過烘烤耐泛黃性和耐久性不如TGIC體系。[1]鋁型材行業目前難以接受HAA體系的這些弊端,或者說是大部分粉末廠家沒有解決這些弊端,所以鋁型材用粉末涂料還是以TGIC體系為主。固化劑TGIC對粉末涂料的耐候性能也有一定的影響。
經過對國內三家銷售量排名靠前的廠家的TGIC進行耐老化檢測,發現它們的耐老化性能基本一致,無較大的差別。因此,在通過固化劑TGIC的選擇上去提高粉末涂料的耐候性,并無多大的意義。3.顏料:顏料對粉末涂料耐候性的影響在原材料中是除了樹脂之外影響*大的因素,因為顏料在使用過程中會褪色,所以對于鋁型材用粉末涂料的顏料的選擇也很重要。市場上即使是用一種顏色的顏料,它的品種非常多,不同品種的色相、著色力、遮蓋力、耐候性、耐熱性等性能千差萬別,這給我們粉末涂料廠家的選擇帶來很大的難度。顏料按化學組成分為無機顏料和有機顏料,它們的優缺點如表2所示。顏料的選擇要從多方面考慮,如顏料的色相、著色力、遮蓋力、耐熱性、耐候耐光性、耐沸水性、毒性等等;而且由于一些顏料可能帶有對樹脂和固化劑起到促進作用的活性基團,所以也要考慮顏料對涂料反應速度、粘度的影響。為了提高粉末涂料的耐候性,顏料要選擇耐光性在7-8級(8級*好),耐候性4-5級(5級*好)的品種,同時耐熱性和耐沸水性要滿足鋁型材行業的使用要求。從表2可知,由顏料本身的性質決定,有機顏料的耐光性和耐候性有限,而無機顏料不夠鮮艷,所以一些鮮艷顏色的粉末大多使用了耐光性和耐候性有限的有機鮮艷顏料,這就是鮮艷顏色的涂膜耐老化色差較大的主要原因。因此,為了保證鮮艷顏色涂膜的耐候性,除了選用耐候性能優異的其他材料,更加要注意顏料的選擇。4.填料:填料的重要功能是添加到粉末涂料中以后,能夠改進涂膜的硬度、剛性和耐劃傷性等物理力學性能,同時有利于改進粉末涂料的貯存穩定性、松散性和帶電等性能。[3]鋁型材粉末涂料中*常用的填料為硫酸鋇,經過對多個廠家的硫酸鋇進行耐老化檢測,發現耐候性能無明顯差別。因此,為了保證涂料的耐候性,必須使用純度高的硫酸鋇作為填料。硫酸鋇進倉前必須經過檢驗,使用10%的鹽酸溶液是*簡單快捷的方法,可以快速檢測出硫酸是否含有碳酸鈣,碳酸鈣會降低涂料的耐候性能,不能作為鋁型材用粉末涂料的填料。5.助劑:在粉末涂料配方中,助劑的用量很少,但在一般粉末涂料配方組成中是不可缺少的成分,而且對涂膜的外觀及某些性能起決定性作用。經過對各國內大型廠家同類助劑進行加速老化對比試驗后,發現不同廠家的流平劑、光亮劑、安息香等對涂膜耐老化性能影響不大;而不同廠家的蠟粉、消光劑對涂膜耐老化的影響較大。因此,為了提高粉末涂料的耐候性,可以考慮使用耐老化性能好的蠟粉和消光劑。二、配方結構:通過粉末涂料中聚酯樹脂的酸值和固化劑羥基當量的計算,設計合適的固化劑用量,并通過加速老化試驗的驗證,使用*佳的固化劑用量,使涂料在固化時能夠充分固化,從而達到*好的耐候性能。
在滿足粉末涂料各項性能的前提下,盡量在配方中減少原材料的種類,特別是對涂膜耐候性起負作用的材料。在不影響涂膜遮蓋力以及硬度、耐磨性的前提下,適當降低配方中的顏料(特別是吸油量大的顏料)和填料的用量,使配方中的顏料能夠在熔融混煉過程充分被樹脂包覆,在涂膜的使用過程中減少顏料的顏色變化,從而達到提高涂膜耐候性的目的。三、制作工藝:粉末涂料制作過程主要包括預混合、熔融擠出、壓片破碎、分級粉碎四個階段,其中預混合、熔融擠出兩個工藝對粉末涂料的耐候性能有很大影響。預混合的作用是為了使粉末涂料配方中的各種原材料組成分散均勻,為熔融擠出打下良好的基礎。為了提高耐候性,在預混合階段,原材料必須按一定的先后順序進行投料,而且投料量控制在混料缸容量的20%-80%,并適當延長混合時間。熔融擠出是為了使粉末涂料組成中的各種成分混合均勻,也就是達到粉末涂料成品中的每個粒子組成成分一樣。為了提高耐候性,在熔融擠出階段,在不出現膠化粒子的前提下,適當提高擠出機溫度(特別是在氣溫較低的情況下),使樹脂熔融成一種流體,保證顏料能有良好的潤濕和獲得*大的剪切力,有利于顏料等的高度分散,使各組分成為一個均勻的體系;在保證生產進度的同時,可以適當降低擠出速度,保證物料有充足的熔融混煉時間;從而提高混煉效果,使粉末涂料中的顏料填料被樹脂充分包覆,而且各種原材料成分粒子分散均勻,特別是固化劑和樹脂能按配方的比例混煉均勻,固化時涂膜能夠充分固化,從而增加涂膜的表面致密性,*終提高粉末涂層的耐候性。四、固化條件:粉末涂料只有充分固化的情況下,樹脂的高分子鏈才會和固化劑完全交聯,各項物理化學性能才會達到*佳狀態,耐候性能也不例外。因此,提高耐候性能必須使粉末涂料充分固化,固化時要控制好溫度和時間。綜上所述,對于提高鋁型材用粉末涂料的耐候性,可參考如下思路:選用耐候性能好且流平不至于太差的樹脂;注意鮮艷顏料、蠟粉、消光劑的選擇;設計有利于提高涂膜耐候性的配方結構;控制好粉末涂料生產工藝。
從粉末涂料本身的角度來看,提高粉末涂層耐候性能主要從原材料、配方結構以及制作工藝等方面著手。一、原材料:粉末涂料主要由樹脂、固化劑、助劑、顏填料等材料組成,這些原材料的耐候性,基本上決定了涂料的耐候性。因此,要提高粉末涂料的耐候性能,首先要選擇耐候性能滿足鋁型材行業要求的原材料,而且這些耐候性合格的原材料也要滿足涂膜的其他性能。當涂膜的各項性能相互間產生沖突時,可以根據客戶的要求側重于某項性能,但是人工加速老化試驗結果要滿足GB 5237.4-2008中加速耐候性的要求。1.樹脂:因為樹脂是粉末涂料的主要成膜物質,是決定粉末涂料性質和涂膜性能的*主要成分,所以樹脂的選擇至關重要。選取市面上大型廠家常用的鋁型材用粉末涂料聚酯樹脂,使用同一配方結構和相同制作工藝分別制粉進行300小時耐老化試驗以及涂膜外觀比較,結果如表1所示。(加速老化條件為8小時光照,4小時凝露循環;UVB-313EL燈,輻照度0.65W/㎡,光照溫度60℃;凝露溫度50℃)由試驗結果可知,樹脂D、F、H在通一系列的樹脂中耐候性較好,但這種樹脂的缺點是分子量大,熔融黏度高,如果應用在平面粉中*終會導致涂膜流平性能差。所以,通過在粉末涂料配方中選用耐候性能好的樹脂來提高平面粉的耐候性能時,必須考慮到涂膜的流平是否會變差,變差之后客戶能否接受。2.固化劑:盡管HAA體系的固化劑環保型眾所周知,但是它的缺點是固化反應有副產物形成,厚噴時容易產生針孔、豬毛孔等弊端,涂膜過烘烤耐泛黃性和耐久性不如TGIC體系。[1]鋁型材行業目前難以接受HAA體系的這些弊端,或者說是大部分粉末廠家沒有解決這些弊端,所以鋁型材用粉末涂料還是以TGIC體系為主。固化劑TGIC對粉末涂料的耐候性能也有一定的影響。
經過對國內三家銷售量排名靠前的廠家的TGIC進行耐老化檢測,發現它們的耐老化性能基本一致,無較大的差別。因此,在通過固化劑TGIC的選擇上去提高粉末涂料的耐候性,并無多大的意義。3.顏料:顏料對粉末涂料耐候性的影響在原材料中是除了樹脂之外影響*大的因素,因為顏料在使用過程中會褪色,所以對于鋁型材用粉末涂料的顏料的選擇也很重要。市場上即使是用一種顏色的顏料,它的品種非常多,不同品種的色相、著色力、遮蓋力、耐候性、耐熱性等性能千差萬別,這給我們粉末涂料廠家的選擇帶來很大的難度。顏料按化學組成分為無機顏料和有機顏料,它們的優缺點如表2所示。顏料的選擇要從多方面考慮,如顏料的色相、著色力、遮蓋力、耐熱性、耐候耐光性、耐沸水性、毒性等等;而且由于一些顏料可能帶有對樹脂和固化劑起到促進作用的活性基團,所以也要考慮顏料對涂料反應速度、粘度的影響。為了提高粉末涂料的耐候性,顏料要選擇耐光性在7-8級(8級*好),耐候性4-5級(5級*好)的品種,同時耐熱性和耐沸水性要滿足鋁型材行業的使用要求。從表2可知,由顏料本身的性質決定,有機顏料的耐光性和耐候性有限,而無機顏料不夠鮮艷,所以一些鮮艷顏色的粉末大多使用了耐光性和耐候性有限的有機鮮艷顏料,這就是鮮艷顏色的涂膜耐老化色差較大的主要原因。因此,為了保證鮮艷顏色涂膜的耐候性,除了選用耐候性能優異的其他材料,更加要注意顏料的選擇。4.填料:填料的重要功能是添加到粉末涂料中以后,能夠改進涂膜的硬度、剛性和耐劃傷性等物理力學性能,同時有利于改進粉末涂料的貯存穩定性、松散性和帶電等性能。[3]鋁型材粉末涂料中*常用的填料為硫酸鋇,經過對多個廠家的硫酸鋇進行耐老化檢測,發現耐候性能無明顯差別。因此,為了保證涂料的耐候性,必須使用純度高的硫酸鋇作為填料。硫酸鋇進倉前必須經過檢驗,使用10%的鹽酸溶液是*簡單快捷的方法,可以快速檢測出硫酸是否含有碳酸鈣,碳酸鈣會降低涂料的耐候性能,不能作為鋁型材用粉末涂料的填料。5.助劑:在粉末涂料配方中,助劑的用量很少,但在一般粉末涂料配方組成中是不可缺少的成分,而且對涂膜的外觀及某些性能起決定性作用。經過對各國內大型廠家同類助劑進行加速老化對比試驗后,發現不同廠家的流平劑、光亮劑、安息香等對涂膜耐老化性能影響不大;而不同廠家的蠟粉、消光劑對涂膜耐老化的影響較大。因此,為了提高粉末涂料的耐候性,可以考慮使用耐老化性能好的蠟粉和消光劑。二、配方結構:通過粉末涂料中聚酯樹脂的酸值和固化劑羥基當量的計算,設計合適的固化劑用量,并通過加速老化試驗的驗證,使用*佳的固化劑用量,使涂料在固化時能夠充分固化,從而達到*好的耐候性能。
在滿足粉末涂料各項性能的前提下,盡量在配方中減少原材料的種類,特別是對涂膜耐候性起負作用的材料。在不影響涂膜遮蓋力以及硬度、耐磨性的前提下,適當降低配方中的顏料(特別是吸油量大的顏料)和填料的用量,使配方中的顏料能夠在熔融混煉過程充分被樹脂包覆,在涂膜的使用過程中減少顏料的顏色變化,從而達到提高涂膜耐候性的目的。三、制作工藝:粉末涂料制作過程主要包括預混合、熔融擠出、壓片破碎、分級粉碎四個階段,其中預混合、熔融擠出兩個工藝對粉末涂料的耐候性能有很大影響。預混合的作用是為了使粉末涂料配方中的各種原材料組成分散均勻,為熔融擠出打下良好的基礎。為了提高耐候性,在預混合階段,原材料必須按一定的先后順序進行投料,而且投料量控制在混料缸容量的20%-80%,并適當延長混合時間。熔融擠出是為了使粉末涂料組成中的各種成分混合均勻,也就是達到粉末涂料成品中的每個粒子組成成分一樣。為了提高耐候性,在熔融擠出階段,在不出現膠化粒子的前提下,適當提高擠出機溫度(特別是在氣溫較低的情況下),使樹脂熔融成一種流體,保證顏料能有良好的潤濕和獲得*大的剪切力,有利于顏料等的高度分散,使各組分成為一個均勻的體系;在保證生產進度的同時,可以適當降低擠出速度,保證物料有充足的熔融混煉時間;從而提高混煉效果,使粉末涂料中的顏料填料被樹脂充分包覆,而且各種原材料成分粒子分散均勻,特別是固化劑和樹脂能按配方的比例混煉均勻,固化時涂膜能夠充分固化,從而增加涂膜的表面致密性,*終提高粉末涂層的耐候性。四、固化條件:粉末涂料只有充分固化的情況下,樹脂的高分子鏈才會和固化劑完全交聯,各項物理化學性能才會達到*佳狀態,耐候性能也不例外。因此,提高耐候性能必須使粉末涂料充分固化,固化時要控制好溫度和時間。綜上所述,對于提高鋁型材用粉末涂料的耐候性,可參考如下思路:選用耐候性能好且流平不至于太差的樹脂;注意鮮艷顏料、蠟粉、消光劑的選擇;設計有利于提高涂膜耐候性的配方結構;控制好粉末涂料生產工藝。
【鋁合金型材,流體管滿足客戶需求】,恒永興金屬材料銷售
有限公司為您提供【鋁合金型材,流體管滿足客戶需求】產品案例,聯系人:李經理,電話:022-86869388、18802286588,QQ:554918566,發貨地:北辰區雙街鎮京津路西(北方實業發展有限公司內)。